Reduce Cost. Accelerate Scalability.
We help companies design and manufacture the most innovative FDA compliant medical devices in the world.
Personalized Time To Market Services™
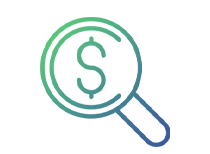
Cost Modeling
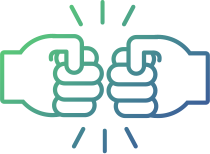
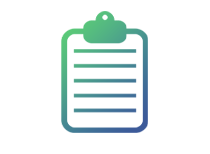
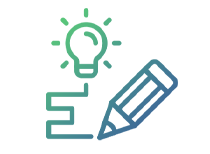
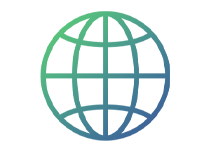
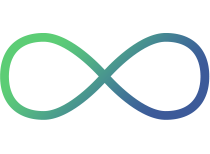
Your Technology. Our Proven Process.
Expert in the commercialization of FDA-compliant medical devices and consumables in the diagnostic, surgical, dental, ophthalmic, aesthetic, rehabilitative, blood management, and imaging markets.
Much More Than a “Contract Manufacturer”
Specialized Services
The Most Advanced Capabilities Imaginable
We are dedicated to providing the highest quality services, with a specialty niche in laser and optically based technologies, consumables and FDA compliant medical device commercialization.
- Design Compliant to 21 CFR 820.30
- Expertise in Optics & Class 4 Lasers
- Surgical Fiber & Sterile Consumables
- Certified Class 7 Clean Room
Strategically Integrated
Vertically Integrated, Where it Matters
In-house printed circuit board assembly (PCBA) ensures quality and control over a critical piece of the manufacturing process, accelerating time-to-market and eliminating delays and margin stack.
- Design and Layout Services
- 24/7 High Speed Line Availability
- AOI, Flying Probe, In-Circuit Test, 3D X-Ray
- Lot 4 Traceability & Silicon Expert™
Scaled Product Launch™
Our Proprietary SPL™ Process
A well-documented phase gate approach to successful new product introduction that focuses on speed, cost reduction, second sourcing, and build efficiency with intense collaboration.
- Elimination of Tribal Knowledge
- Documentation Verification & Validation
- Serialization & Traceability Assessment
Infinite Capacity™
Never Miss a Market Opportunity™
Our commitment to providing the resources, facilities and equipment to handle unthinkable and unpredictable market demand, enabling you to say YES to every market opportunity.
- 24/7 Production Availability
- Finished Goods Storage & Distribution
- Aftermarket & Refurbishment Services
Compliance & Certifications
Process and Results that Meet or Exceed All Expectations
Commercialize products compliantly with all applicable standards, statutory, and regulatory requirements. We have unmatched experience working with a range of regulatory agencies including CSA, CE, TUV, and IEC.
At the end of the day, what we really build is TRUST.
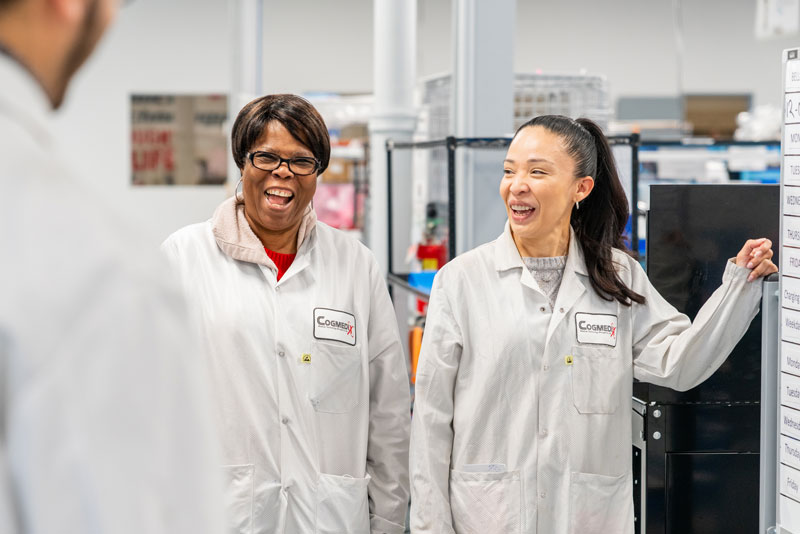